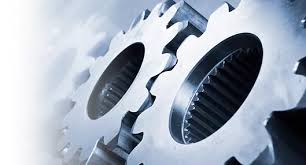
- 1-) İşleme Termoplastikleri
- 2-) İşleme Termosetleri
- 3-) İkincil Üretim Süreçleri
- 4-) Ön İşleme Teknolojileri
- 5) Geri Dönüşüm
- 6) Plastik Sektöründe Statik Kontrol Problemleri
- 7) Proses Maliyetleme Rehberi
1.1 Üflemeli Film
Genel Açıklama:
Süreç, bir plastik malzemenin dairesel bir kalıptan ekstrüzyonunu ve ardından “kabarcığa benzer” bir genleşme işlemini içerir.
Kullanılan Tipik Malzemeler:
Temelde polietilenler (HDPE, LDPE ve LLDPE) ancak bu reçinelerle karışımlar olarak veya çok katmanlı film yapısında tek katmanlar olarak çok çeşitli diğer malzemeler kullanılabilir. Bunlar PP, PA ve EVOH’dir
Üretilen Tipik Ürünler:
Sanayi ambalajları (örn., Shrink film, streç film, çanta filmi veya konteyner gömlekleri), Tüketici ambalajları (ör. Dondurulmuş ürünler için ambalaj filmi, taşıma ambalajı için shrink filmi, gıda ambalaj filmi, ambalaj torbaları veya form, doldurma ve mühür Bariyer filmi, tıbbi ürünlerin ambalaj filmleri, Tarım filmi (örn. sera filmi, kırpma filmi, silaj filmi, silaj streç filmi), laminasyon filmi (örn. süt veya kahve ambalajında kullanılan alüminyum veya kağıt laminasyonu) film).
1.2 Ekstrüzyon Şişirme
Genel
Açıklama Üfleme kalıplama makinesi, polimerin plastikleştirilmesi için standart bir ekstruder varil ve vida tertibatı üzerine kuruludur. Erimiş polimer, bir parison adı verilen içi boş (genellikle dairesel) bir boru kesiti olarak ortaya çıkmak için dik açılı ve bir kalıptan geçirilir.
Kullanılan Tipik Malzemeler:
Polipropilen (PP), Polietilen (PE), Polietilen – Tereftalat (PET) ve Polivinil klorür (PVC)
Üretilen Tipik Ürünler:
Şişeler ve konteynerler, Otomotiv yakıt tankları, Havalandırma Kanalları, Sulama Tenekeleri ve Tekne Çamurlukları vb.
1.3 Ekstrüzyon Profilleri ve Tablosu
Genel Bilgiler
Enjeksiyon kalıplama ile birlikte, Pro-file Plastik malzemelerin ekstrüzyonu, plastik malzemelerin oluşturulmasında yaygın olarak kullanılan bir yöntemdir. Plastik hammadde, ısıtılmış döner vidaların hareketi ile hem eritilir hem de hareket ettirilir. Sürekli bir işlemdir ve bu nedenle bir ürünün uzun uzunluklarını üretebilir. Boru ve contalar gibi uygulamalar için idealdir. Bununla birlikte, sık sık sürekli ekstrüzyon uygulama uzunluklarına kesilir
Kullanılan Tipik Malzemeler:
HDPE, PVC ve PTFE dolu PVC
Üretilen Tipik Ürünler:
Kar Drenajı Boruları, Hayvan Besleme Kanalları, Kablo Demeti, Kapı Contaları, Işık Difüzörleri, Elektrikli Boru ve Kablo Koruyucu, Yağmur Suyu Boruları ve Kanalizasyon, Facia & Soffit Kesitleri, Perde Yolu, Buzdolabı Contaları, Kenar Kenar Panjuru, Karavan Pencere Çevresi, Bahçe Çitleri ve Decking, Kan Damla Tüpleri ve Kateter Tüpleri, Daldırma Boruları, Gaz Boruları, Su Boruları, Zemin Boruları ve Pencere, Kapı ve Konservatuar Kesitleri
1.4 Enjeksiyon Üfleme Kalıplama
Genel Bilgiler
Enjeksiyon üfleme kalıplaması, büyük miktarlarda içi boş nesnelerin üretimi için kullanılır. Başlıca uygulamalar şişeler, kavanozlar ve diğer kaplardır. Enjeksiyon üfleme kalıplama yöntemi, ekstrüzyon üfleme kalıplama ile karşılaştırıldığında üstün görsel ve boyut kalitesinde şişe üretir. Bu yöntem, dar ve geniş ağızlı kaplar için idealdir ve flaşsız olarak tamamen bitmiş halde üretilmektedir.
Tipik Kullanılan Malzemeler:
polietilen (düşük yoğunluklu) LDPE (LLDPE), Polipropilen (PP), Polietilen – terefitalat (PET), polivinil klorür (PVC), polietilen (yüksek yoğunluklu) HDPE)
Üretilen tipik Ürünler:
Plastik şişeler
1.5 Enjeksiyonluk Kalıplama
Genel Bakış
Enjeksiyon kalıplama (veya US yazımını kullanmak için kalıplama), ekstrüzyon ile birlikte plastik ürünler üretmenin başlıca süreçlerinden biri olarak görülüyor. Hızlı bir işlemdir ve yüksek hassasiyetteki mühendislik bileşenlerinden tek kullanımlık tüketim mallarına kadar çok sayıda özdeş ürün üretmek için kullanılır.
Tipik Malzemeler:
Akrilonitril-Butadien-Stiren (ABS), Naylon (PA), Polikarbonat (PC), Polipropilen (PP) ve Polistiren (GPPS)
Üretilen Tipik Ürünler:
Elektrikli alet gövdeleri, Telefon ahizeleri, Televizyon dolapları, Elektrik şalterleri, DVD’ler, Otomotiv tamponları, Otomotiv panoları, Pil Muhafazaları, Şırınga, İlaç İnhalasyon Ünitesi, Tek kullanımlık traş makinesi, çamaşır yıkama kaseleri, Tekerlekli kaplar, Kasalar / Geri Dönüşüm kutuları ve Şişe Kapakları / Kapakları
1.6 Enjeksiyon Döküm (Gaz Yardımlı)
Genel Bakış
Gaz Yardımlı Kalıplama veya (Gazla Mücadele Kalıplama, ABD yazım hatlarını veya Gaz Enjeksiyon Kalıpcağını ortak bir referans terimi olarak kullanmak için kullanılan) son yıllardaki gelişmeler, enjeksiyonla kalıplanmış bileşenler üretme yolunda ilerlemeler sağlamıştır. Süreç sayesinde gelişmiş kalite, azaltılmış çevrim süreleri ve bileşen ağırlığı indirimleri sağlanabilir.
Kullanılan Tipik Malzemeler:
Akrilonitril-Butadien-Stiren
Üretilen Tipik Ürünler:
Elektrikli alet gövdesi, Telefon
1.7 Enjeksiyon Streç Şişirme
Genel Bakış
Enjeksiyon germeli üfleme kalıplama, yüksek kaliteli kapların üretimi için kullanılmaktadır.
Kullanılan Tipik Malzemeler:
Polietilen – Tereftalat (PET)
Üretilen Tipik Ürünler:
Karbonatlı ve alkolsüz içecek şişeleri, Pişirme yağı konteynırları, Zehirli kimyasal kutular Sağlık ve ağız temizleme ürünleri ve Banyo ve tuvalet ürünler
1.8 Döküm Kalıplama
Genel Bilgiler
Ek parçalar kalıplama işlemi sırasında birleştirilebilir veya bir kalıplama sonrası işlem olarak eklenebilir. Döküm işleminin bir parçası olarak dahil edildiğinde, insertler ya robot yardımıyla ya da proses operatörü ile yüklenebilir. Ekler son kalıplama işlemi olarak uygulanıyorsa, bunlar genellikle kalıplama işleminden sonra her zaman uygulanabilir. Bazı durumlarda, bir dizi kalıp sonrası operasyonların bir parçası olarak yerleştirilirler. Bu, ekleme maliyetini en aza indirmeye yardımcı olur. İşlem hızının (ve ekonominin) temelleri ve sürecin tekrarlanması, ekin ne zaman uygulanacağına karar verirken akılda tutulmalıdır. Çevrim süresinin atıştan kullanıma kadar değişmesine izin vermek iyi bir uygulama değildir; bu kalite üzerinde olumsuz bir etkisi olabilir
1.9 Plastiklerin İşlenmesi
Bir plastik bileşen belirtildiğinde ve kullanılacak numaralar büyük olmadığında, bileşeni parça işleme daha ekonomik hale gelir.
1.10 Kalıplama Genleştirilmiş Polipropilen (EPP)
Genel Bakış
EPP üstün enerji emme, çoklu darbe direnci, ısı yalıtımı, yüzdürme, su ve kimyasal direnç, son derece yüksek ağırlık / ağırlık oranı ve% 100 geri dönüştürülebilirlik gibi benzersiz özellikler sunan çok yönlü kapalı hücreli bir boncuk köpüktür. EPP, litrede 15 ila 200 gram arasında yoğunlukta geniş bir yelpazede yapılabilir ve bunlar litrede 18 ila 260 gram arasında değişen yoğunluklara dönüştürülür. Bireysel boncuklar, buhar kanalı kalıplama prosesi ile nihai ürün formuna kaynaştırılarak güçlü ve hafif bir şekil elde edilir.
1.11 Kalıplama Genleştirilmiş Polistren (EPS)
Genel Bilgiler
Genişletilmiş polistiren (EPS), bir takım uygulamaların üretimi için kullanılmaktadır. Bununla birlikte, önemli uygulama, tüketici elektroniği ürünleri ve beyaz eşyalar için koruyucu bir ambalaj olarak görülüyor. Mükemmel ısı yalıtımı ve mekanik koruma özellikleri, balıkları ve diğer gıda maddelerini paketlemek için idealdir. EPS ayrıca tohumluk tepsileri olarak bahçecilik uygulamalarına da sahiptir. Genişletilmiş polistren ambalajın olağanüstü şok emiciliği, geniş bir ürün yelpazesinin korunmasını sağlar.
1.12 Proses Soğutma
Genel Bakış
Plastik işleme makinelerinin soğutulması veya soğutulması gerekliliği esas olarak termoplastik malzemeler ile ilgilidir. Oda sıcaklığında termoplastik malzemeler (polipropilen, naylon ve PET vb.) Katıdır. Onları şekillendirmek için öncelikle erimiş sıcaklığına ısıtılmalıdırlar. Erimiş halde, daha sonra yeni bir şekle getirilmek üzere manipüle edilebilirler (enjeksiyon kalıplı, haddelenmiş vb.). Yeni şekillerine dönüştüğü zaman onları katılaştırmak için soğutulmaları gerekir. Malzemeden, alet takımından ve şekillendirmeyi yapan makineden önemli miktarlarda ısı enerjisi çıkartılmalıdır.
1.13 Döndürme Kalıplama
Genel Açıklama
Rotasyonel kalıplama (genellikle Rotamoulding veya Rotomoulding olarak anılacaktır) içi boş plastik ürünler üretmek için kullanılan bir süreçtir. Ek kalıplama sonrası işlemler kullanarak, kompleks bileşenler üretilebilir ve bu yöntem diğer kalıplama ve ekstrüzyon uygulamaları ile etkili bir şekilde rekabet edebilir.
Rotasyonel kalıplama, polimer kalıba yerleştirildikten sonra ısıtma, eritme, şekillendirme ve soğutma aşamalarını oluşturduğu için diğer işleme yöntemlerinden farklıdır, bu nedenle şekillendirme sırasında herhangi bir dış basınç uygulanmaz.
Bu, aşağıdaki avantajları sağlar Ekonomik olarak üretilen büyük ürünler, Minimum tasarım kısıtlamaları, Gerilmesiz ürünler, Polimer kaynak hatları yok ve Nispeten düşük kalıp maliyetleri.
büyük bir resmi görmek için buraya tıklayın
1.13.1 Rotasyonel Kalıplama (Materyal)
genel bakış
Rotasyonel Kalıplama (Amerikan sp. Kalıplama), çok yönlü ve üretilebilen şekillerde ve ürünlerde hemen hemen sınırsız olan benzersiz bir prosestir.
Tasarımcılar ve kalıpçılar, zorlayıcı uygulamaları daha fazla karşılamak için sınırları zorluyor ve daha geniş bir malzeme çeşitliliği talep ediyorlar.
İşlem, malzemenin enjeksiyon ve üfleme kalıplama gibi diğer işlemlere kıyasla çok daha uzun ısı döngüsüne tabi tutulmasını gerektirdiğinden, Rotasyonel kalıplama malzemeleri, malzeme özelliklerinin oksidasyonunu ve parçalanmasını önlemek için gelişmiş bir ısı dengeleme katkı paketi gerektirir. Buna ek olarak, verilen Rotasyonel kalıplama sınıflarının hepsinde UV stabilizasyon katkı paketi bulunması, bu nedenle dış mekan ve iç mekan uygulamaları için idealdir. Dolayısıyla, diğer prosesler için genel piyasada bulunan malzemeler Rotasyonel kalıplama için kullanılmamalıdır.
Bu nedenlerden dolayı ve Rotasyonel kalıplama işlemi için dünya çapında kullanılan daha düşük hacimlere bağlı olarak, mevcut malzemeler termoplastik tedarikçilerle sınırlıdır.
1.14 Yapısal Köpük
Genel
Yapısal Köpük, hücresel bir göbeği olan enjeksiyon kalıplama işlemi ile yapılan termoplastik enjeksiyon kalıplama bileşenlerini tanımlamak için yaygın olarak kullanılan bir terimdir. Bir hücresel plastik, dış yüzeyin iç katlardan daha yoğun olduğu plastiktir. Dökümün çekirdeği petekli bir yapıdadır ve dış yüzeyden daha az yoğundur. Kombinasyon, yapısal olmayan köpük (kompakt) kalıplarla karşılaştırıldığında yüksek bir sertlik oranının kalıplanması ile sonuçlanır.
1.15 Termoform
Genel Açıklama
Thermoforming, Vakumla Şekillendirme ile yakın benzerliklere sahiptir, ancak yumuşatılmış tabakanın hava basıncı ve tıkacın yardımıyla şekillendirilmesi daha fazla kullanılmaktadır. Süreç her zaman otomatiktir ve Vacuum Forming işleminden daha hızlı döngü sürelerine erişilir. Bu yöntemle sadece termoplastik levha işlenebilir.
1.16 Vakum Oluşturma
Genel Açıklama
Termoform, plastik malzemelerin işlenmesinde kullanılan en eski ve en yaygın yöntemlerden biridir. Vakumla şekillendirilen ürünler çevremizde olup günlük hayatımızda büyük bir rol oynamaktadır. Proses, bir plastik tabakanın yumuşak olana kadar ısıtılmasını ve daha sonra bir kalıba dökülmesini içerir. Levhayı kalıba emen bir vakum uygulanır. Levha daha sonra kalıptan dışarı atılır. Gelişmiş şekli ile vakum şekillendirme prosesi sofistike pnömatik, hidrolik ve ısı kontrollerini kullanır, böylece daha yüksek üretim hızları ve daha ayrıntılı vakum form uygulamaları sağlar.
1.17 Diğer Ekstrüzyon Prosesleri
Döküm Filminin Ekstrüzyonu
Tanım: Bir silt kalıptan eriyik ince bir film üretmek için bir rulo ya da bant üzerine beslenir.
Dikkat çeken noktalar: Çok ince film üzerinde parlak parlaklık.
İnce Tabaka / Film Kalenderleme
Tanımı: Bir dizi silindirden geçerek hassas ince tabaka / film imalatı.
Uygulamalar: Döşeme için dekoratif tabaka. Koruyucu sac. Streç sarma filmi.
Dikkate değer puanlar: Yalnızca uzun mesafeler için.
Koekstrüzyon / Laminasyon
Tanımı: Farklı materyal katmanlarıyla levha üretimi.
Uygulamalar: Ambalaj, buzdolabı kapıları, açık hava uygulamaları.
Dikkate değer hususlar : Levha özelliklerin dengesini geliştirmiştir.
2.1 Pultrüzyon
Genel
Açıklama Pultrüzyon işlemi, sürekli reçine emdirme sistemi vasıtasıyla (takozlar veya mat / fitil formlarında) takviye çekerek başlatılır. Her elyaf özel olarak formüle edilmiş bir reçine ile kaplanır; işlem lif takviyesinin tam “ıslanmasını” sağlamak için kontrol edilir. Fazla reçine daha sonra sıkışan havayı atmak ve lifleri sıkıştırmak için çıkarılır.
Kaplanmış fiberler, takviye hizalamak ve parçayı, ısıtılmış kalıba girmeden önce arzu edilen şekle göre önceden şekillendirmek üzere önceden hazırlama kılavuzlarından geçirilir. Nihai ürünün şekli ve boyutları en sonunda kalıp kesiti ile belirlenir. Kalıbın sıcaklığı, bileşimin tamamen kürlendiğinden emin olmak için dikkatlice kontrol edilir, reaksiyon hızı kalıptaki ısıtma ve soğutma bölgeleri tarafından kontrol edilir.
büyük bir resmi görmek için buraya tıklayın
2.2 Reçine Transfer Kalıplama
Genel Bakış
RTM düşük basınçlı bir kalıplama işlemidir, burada karışık bir reçine ve katalizör, bir fiber paketi veya preform içeren kapalı bir kalıba enjekte edilir. Reçine kürlendiğinde kalıp açılabilir ve bitmiş bileşen çıkarılır.
Polyester, vinilester, epoksi, fenolik ve metil metasilatlar gibi çeşitli reçine sistemleri kullanılabilmekte, gerekirse alüminyum trihidratlar ve kalsiyum karbonatlar gibi pigmentler ve dolgu maddeleri ile birleştirilmektedir.
Fiber paketi cam, karbon, arimid veya bunların bir kombinasyonu olabilir. Çok çeşitli ağırlık ve stiller mevcuttur.
2.3 SMC / DMC Kalıplama
Genel Bilgiler
Materyaller Nasıl Elde Edilir DMC ve BMC
DMC / BMC bileşiklerinin imalatı yığın prosesi. Malzemeler, kıyılmış cam elyafı, reçine, mineral dolgu maddeleri, katalizörler ve bir kalıptan çekiş DMC Conduit Box aracı özel bir karıştırıcıya yüklenir. Karıştırıcıdan gelen çıktı, daha sonra bir halat tipi ekstrüzyonla haddelenen bir sürü formundadır.
büyük bir resmi görmek için buraya tıklayın
SMC SMC
imalatı sürekli bir hat içi işlemdir. Malzeme plastik bir filmle hem üstte hem de altta kaplanır. Reçine, stiren, ısı ile aktive edici katalizörler, inert dolgu maddeleri, serbest bırakma maddeleri ve koyultma maddeleri içeren bir macun hazırlanır. Hamur alttaki filmin bir SMC Bağlantı Kutusu üzerine eşit olarak yayılır. Kırpılmış cam elyafı macun üzerine rastgele biriktirilir. Üst film verilir ve sandviç önceden belirlenmiş bir kalınlığa haddelenir. Levha 48 saat boyunca olgunlaşır.
2.4 Diğer GRP Kalıplama Teknikleri
El Yığılması / Yumru Düzleştirme
Genellikle, cam elyaf hasırın sıvı poliester karışımı ile emprenye edilmesini içerir. El Yerleştirme, parça geometrisini tanımlayan bir alet veya kalıp üzerine ardışık tabakalarda kompozit malzemeleri elle uygulayarak bileşik yapılar üretmenin bir yöntemidir. Püskürtme yatırması esas olarak matetialin kalıba püskürtülmesini içeren bu proses üzerinde bir varyanttır. Bir ‘Jel Kat’ eklenebilir, kalıp tarafında iyi bir yüzey sağlar.
Sıkıştırma Kalıplama
Sıkıştırma Kalıplama, belki de termosetlerin kalıplanması için bir sonraki en yaygın tekniktir. Bileşik veya harman kalıp içine yerleştirilir ve buharla ısıtılmış bir presin plakaları içerisinde basınç altında ısıtılır. Reaksiyon tamamlandığında, ürün soğutulur ve dışarı atılır. Sıkıştırma kalıplama, kesintisiz işleme karşıt olarak bir partidir. Pres kalıplama Malzeme, genelde bir ‘pre-preg’ formunda düz plakalarla büyük bir prese yüklenir. Karışımı reaksiyona sokmak ve nihai üründe dönüştürmek için ısı ve basınç uygulanır. Bu teknik büyük kalıplar ve bazı sac ürünler için kullanılır. Sıkıştırma kalıplama işleminde olduğu gibi, bu oldukça yavaş bir işlemdir.
Reçine Transferli Kalıplama
Erimiş reçine, bir mürekkep püskürtmesinin basınca göre reçinenin erime noktasının üzerinde bir sıcaklıkta olan bir kalıba aktarılır. Yüksek sıcaklık, yüksek akış uzunluğu, yüksek duvar kalınlığı oranlarına sahip kalıpların doldurulması ve büzülme telafisi için önemlidir.
Pultrüzyon
Pultrüzyon, çubuklar, borular ve sürekli kesitlere sahip yapısal biçimlerdeki kompozitler üretmek için sürekli bir işlemdir. Takviye, reçine emdirme banyosundan geçirildikten sonra, arzu edilen kesit oluşturmak için şekillendirme kalıbı boyunca çekilir; Kürleme laminatın kesitten ayrılmadan önce gerçekleşir.
Filament Sarma
Oldukça otomatik hale getirilebilen ve nispeten düşük malzeme maliyetleriyle tekrarlanabilen sürekli, otomatikleştirilmiş bir imalat yöntemi. “Kafası” (elyaf uygulama aleti) yatay eksende dönerken mandrelin uzunluğu boyunca öne ve arkaya hareket ederken elyafı alet üzerine yerleştirirken, mandrel adı verilen uzun silindirik bir alet, uç destekler arasında yatay olarak asılmıştır. önceden belirlenmiş bir konfigürasyon. Çoğu uygulamada, filament sarma aparatı, malzeme materyalin mandreline değmesinden hemen önce elyaf malzemesini bir “banyoda” geçirir.Buna “ıslak sarım” denir. Reçine ile önceden emprenye edilmiş sürekli lif, aynı zamanda, yerinde reçine banyosu ihtiyacını ortadan kaldırarak da sarılabilir. Biraz farklı bir işlemde, elyaf reçine olmadan sarılır (“kuru sargı”).
Reaksiyon Enjeksiyon Kalıplama
Bu prosedürler poliamidler (termoplastik) veya poliüretanlar, doymamış polyesterler, epoksiler ve fenolikler (termoset) gibi kalıplama esnasında reaksiyonla üretilen polimerler üretir. RIM, enjeksiyon veya transfer kalıplama kullanılarak yapılabilir.
Enjeksiyonluk
termosetlerin enjeksiyon dökümü Temel olarak bu, termoplastikler için kullanılanla aynı işlem olup, plastikteki sertleşmeyi önlemek için modifiye edilmiştir. Kullanılan malzemeler yaygın olarak Hamur veya Dökme Kalıp Bileşikleri (DMC veya BMC) olarak bilinir. Levha şekli olarak, Levha Döküm Bileşimi (SMC) olarak bilinirler. Elektrikli anahtar ve sigorta kutuları, ev elektrik malzemeleri, mikrodalga kaplar ve sofra takımları vardır. İş makinesi gövdeleri, gaz ve elektrik sayacı kutuları ve bulaşık antenleri için de kullanılır.
3.1 Kaynak
Genel Bakış
Plastik ürünler her zaman tek parça halinde üretilemez. Tasarım ve takım kısıtlamaları bazen ürünü iki veya daha fazla parça olarak kullanmanın ekonomik ve / veya avantajlı olmasını sağlar. Parçaların kalıptan sonra birleşmesi, bir son çözüme ulaşmak için bir yöntem sağlar. Hangi Yöntem? Birleştirme yönteminin seçimi sonuçta parça malzemesine, geometrisine ve boyutuna, proses kabiliyetine, istenen hacim ve çevrim süresine bağlıdır. Sermaye maliyetleri gibi diğer hususlar seçim üzerinde bir önem taşımaktadır.
Uygulamalar:
Tasarım ve takım kısıtlamaları bazen ürünü iki veya daha fazla parça olarak kullanmanın ekonomik ve / veya avantajlı olmasını sağlar. Parçaların kalıptan sonra birleşmesi, bir son çözüm elde etmenin bir yolunu sağlar.
3.2 Termoplastik Üretim
Genel
Açıklama Termoplastiklerin Endüstriyel Üretim Süreci, birincil imal edilen sac, boru, astar ve kalıplanmış veya oluşturulmuş profillerin uyumlu malzemeler ve kaynak yöntemleri kullanılarak nihai bir ürün veya sistem üretmek üzere kullanılması ve daha fazla modifikasyonu olarak tanımlanabilen ikincil bir üretim sürecidir. çeşitli endüstriyel uygulamalarda bir hizmet, tesis, sistem veya proses sağlamak üzere termoplastik olmayan malzemelerle bağlantılı olarak veya termoplastik olmayan malzemelerden ayrı olarak kullanılabilir.
4.1 Polimerin Kurutulması
Genel Bilgiler
Çiğ plastik malzemelerin çoğu kuru görünüyor. Bununla birlikte, her şey her zaman göründüğü gibi değildir. Polikarbonat, Naylon ve PET gibi higroskopik malzemeler sadece üç taneyle çevreleyen havadan nem çeker. Dolayısıyla, işlemciye ulaştığı andan itibaren “kuru” olarak imal edilmesine rağmen, nem içeriği olacaktır. İlgili prosesler Nem Alma Kurutucuları, Döner Tekerlek Kurutucuları, Alçak Basınçlı Kurutucular ve Vakum Kurutucular
4.2 Harmanlama ve Dozlama
Genel Bakış
Dozaj, işleme makinesine giren materyal akışına konsantre renk gibi seçilen bir malzeme unsurunu getirir. Bununla birlikte, harmanlama, sadece işleme makinasına giren katkı maddelerini değil, tarifi için gereken tüm bileşenleri kontrol eder.
Genel Bilgiler
Bütün plastikler geri dönüşümlüdür, ancak geri dönüşüme tabi tutulmaları hem ekonomik hem de lojistik faktörlere bağlıdır. Değerli ve sınırlı bir kaynak olarak, ilk kullanımdan sonra çoğu plastik için en uygun kullanım, tercihen tekrar dönüştürülebilen bir üründe geri dönüştürülmesidir. İngiltere, her yıl yaklaşık 5 milyon ton plastik kullanıyor ve bunun yaklaşık% 19’u şu anda geri kazanılıyor veya geri dönüştürülüyor. Bu rakamın 2010’da İngiltere’de tüketilen tüm plastiklerin% 25’inden fazla olması bekleniyor.
Uygulamalar:
Tüm plastikler geri dönüştürülebilir. Geri dönüştürülme derecesi hem ekonomik hem de lojistik faktörlere bağlıdır
Plastik endüstrilerinde statik elektrikle ilgili sorunlar çoktur. Statik yükün sorun yaratabileceği süreçler enjeksiyon kalıplama, üfleme kalıplama, termoform oluşturma, döner kalıplama, parçaların taşınması ve toplama ve montaj işlemleri içerir.
Yüksek statik yük düzeylerinden kaynaklanan birincil sorunlar şunlardır:
- Toz Çekimi ve Kirliliği
- Proses Kontrol ve Kalite Sorunları
- Operatör Şokları